A Comprehensive Approach to Resolving Stretch Wrap Equipment Repair Obstacles
You understand that stretch cover machines are critical for preserving efficiency in product packaging operations. Concerns can emerge that interfere with productivity. What are the finest strategies to guarantee your devices run smoothly?
Recognizing Usual Stretch Wrap Machine Issues
When you depend on stretch wrap makers for reliable packaging, it's critical to acknowledge common issues that can interfere with procedures - stretch wrap machine repair. One common problem is inconsistent tension, which can result in poor covering and endangered tons stability. If you discover the film isn't adhering effectively, look for worn-out rollers or improper settings
Another problem you could encounter is film damage, often created by incorrect film type or maker breakdowns. Regularly examine the maker for signs of wear and tear to stop this.
Furthermore, keep an eye on movie accumulation or jams, which can halt production. Usually, this occurs because of imbalance or particles in the device.
Last but not least, inappropriate sealing can lead to loads coming apart throughout transportation. Make sure your device is adjusted properly to maintain the integrity of your packages. By staying watchful and dealing with these issues immediately, you can assist in smoother operations.
The Relevance of Normal Preventative Maintenance
Normal preventative upkeep is important for maintaining your stretch cover equipment running smoothly and effectively. By consistently examining and servicing your equipment, you can spot potential issues before they intensify right into pricey repair work. This proactive approach not only extends the life-span of your equipment yet likewise guarantees that it operates at peak performance.
You must arrange normal evaluations to clean, lubricate, and replace used parts. Keeping your maker calibrated aids maintain ideal wrapping quality, decreases waste, and enhances performance. Furthermore, recording upkeep tasks creates a trusted history that can notify future choices.
Don't forget the value of training your staff on maintenance finest techniques. When everybody comprehends exactly how to look after the device, you lessen the risk of operator mistake resulting in break downs. Simply put, dedicating to routine preventative upkeep is a clever financial investment that settles in reduced downtime and boosted performance in your operations.
Troubleshooting Strategies for Quick Repairs
Efficient fixing strategies can greatly reduce downtime when your stretch cover equipment runs into problems. Is the machine not wrapping properly or is it making unusual sounds?
Next, check the equipment's settings and controls; in some cases, a straightforward change can resolve the problem. Check the movie tension and placement, as inappropriate configuration can lead to covering failures. Do not overlook electrical connections; loosened or damaged cables can interfere with capability.
If you're still facing challenges, take into consideration running diagnostic tests if your equipment has that capacity. File each action you take, as this can aid in future troubleshooting and fixings. Ultimately, do not wait to talk to a specialist if you can't solve the problem rapidly. Effective troubleshooting keeps your procedures running smoothly and minimizes expensive hold-ups.
Educating Operators for Effective Machine Use
To ensure your stretch cover machine runs at peak effectiveness, proper training for drivers is important. When operators understand the equipment's functionalities, they can maximize its prospective and minimize downtime. Begin by providing them with complete handbooks that outline operational treatments and safety and security protocols. Hands-on training is vital; it enables drivers to familiarize themselves with the maker's controls and setups.
Motivate them to exercise under supervision, resolving any kind of concerns or worries they may have. Regularly set up refresher course courses can maintain their skills sharp and aid them adjust to any kind of updates or changes in innovation.
Furthermore, instill a society of accountability by encouraging operators to report problems or recommend enhancements. This aggressive strategy not only enhances their self-confidence but likewise adds to the overall performance of your operations. With trained drivers, you'll see fewer mistakes and raised performance, guaranteeing your stretch cover machine remains a beneficial possession.
Developing a Solid Interaction Network Between Teams
Well-trained drivers can just carry out at their finest when there's a strong interaction channel between teams. Efficient communication removes misconceptions and assurances every person's on the exact same page pertaining to equipment operations and repair work needs. Urge regular check-ins and meetings to talk about issues, share understandings, and address worries.
Using innovation, like messaging apps or collective systems, can improve real-time communication, making it simpler to report troubles and share updates swiftly. Designating clear functions and responsibilities promotes responsibility, enabling team members to get to out to the appropriate individual when issues develop.
Furthermore, creating an open setting where everybody really feels comfortable sharing responses can cause ingenious solutions. By focusing on communication, you're not just boosting device efficiency; you're likewise building a cohesive team that functions with each other effortlessly. This collaborative spirit eventually brings about quicker repair work and reduced downtime, benefiting the entire procedure.
Purchasing Top Quality Replacement Parts
When it concerns maintaining your stretch cover equipments, spending in top quality substitute parts is vital for making certain trustworthy efficiency and minimizing downtime. Affordable choices might my latest blog post seem alluring, yet they usually lead to even more considerable issues down the line, costing you extra in fixings and shed efficiency. By selecting high-quality parts, you're not just dealing with an issue; you're enhancing the total effectiveness of your tools.
Additionally, high quality parts are normally manufactured to stricter requirements, which suggests they'll fit much better and operate more reliably. This reduces the chance of unanticipated break downs, enabling your operations to run smoothly. Reputable suppliers often provide warranties, providing you tranquility of mind in your investment.

Evaluating Performance Information for Continuous Improvement
To boost your stretch cover machine's performance, you require effective information collection methods. By examining performance metrics, you can determine areas for improvement and increase efficiency. Determining these possibilities not only enhances procedures however additionally reduces downtime and repair work prices.
Data Collection Methods
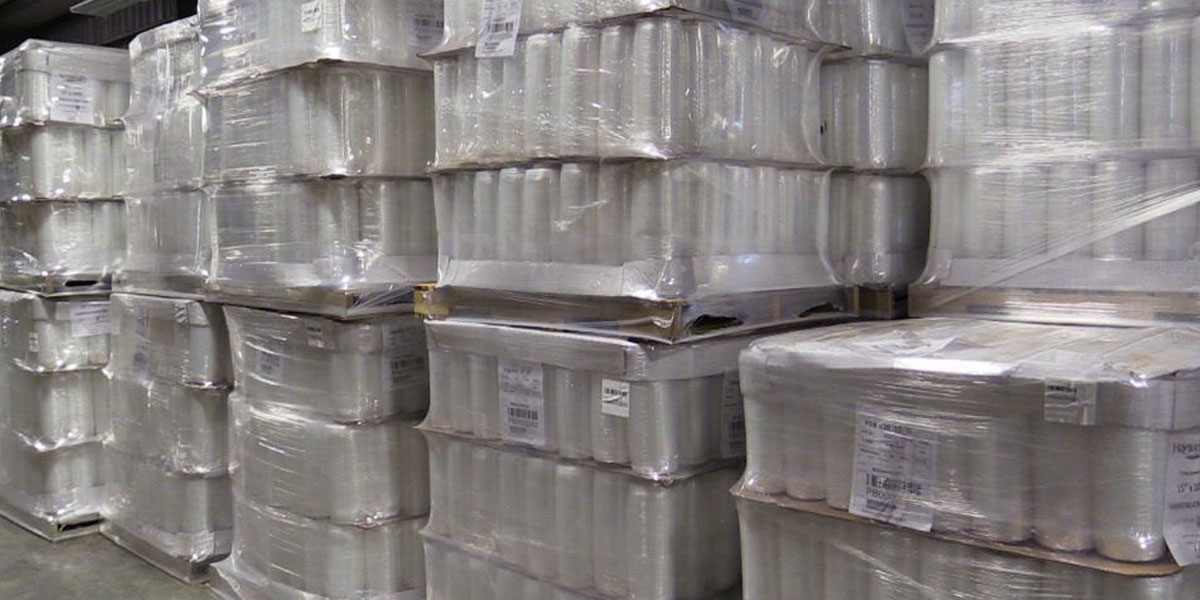
Efficiency Metrics Assessment
While reviewing performance metrics, it's essential to concentrate on specific information factors that directly influence your stretch cover device's performance. Begin by tracking cycle times, as they reveal how rapidly your device operates under regular problems. Monitor downtime incidents to identify patterns or persisting concerns that may need dealing with. Maintain an eye on movie usage, ensuring you're not squandering material, which can impact prices and performance. In addition, evaluate outcome top quality by examining for disparities in the wrapping process. By evaluating these metrics frequently, you can determine areas needing focus and take positive actions. This continuous analysis helps boost performance, minimize costs, and ultimately improve your maker's longevity, leading to a more effective wrapping procedure on the whole.
Determining Improvement Opportunities
As you examine efficiency data, you can reveal important improvement opportunities that enhance your stretch cover equipment's performance. Seek patterns in downtime, cycle times, and wrap high quality. By determining patterns, you'll see which locations need attention. If frequent break downs correlate with certain operating problems, you can change processes to minimize these problems. In addition, contrast your data against sector standards to determine your efficiency. Involve your team in conversations about the searchings for; their insights can reveal sensible remedies. Carrying out small changes based on this analysis can lead to considerable gains in productivity. Consistently reviewing and updating your performance information will certainly ensure constant improvement, maintaining your procedures running smoothly and effectively.
Frequently Asked Questions
Just How Can I Tell if My Device Needs a Fixing or Simply Maintenance?
To tell if your machine needs repair service or simply upkeep, listen for unusual noises, look for inconsistent efficiency, and evaluate for noticeable wear. If issues continue after maintenance, it's likely time for a repair work.
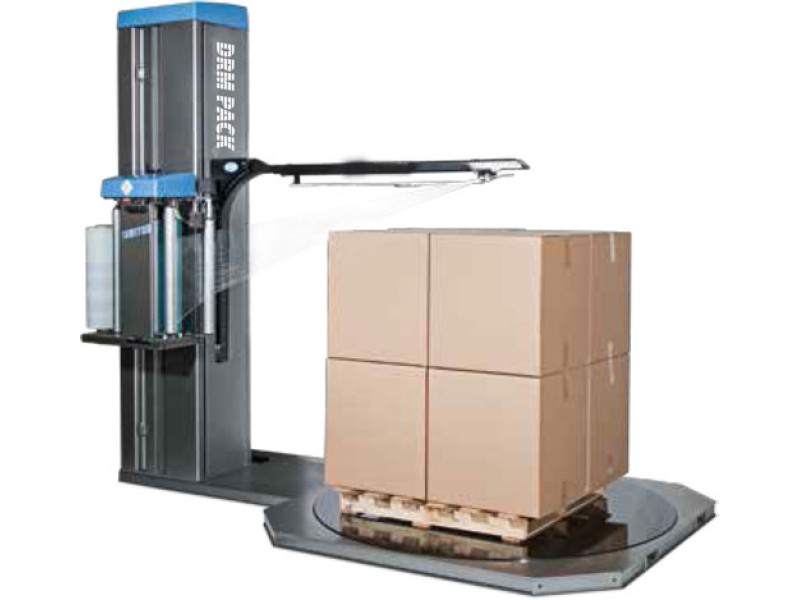
What Is the Typical Life-span of a Stretch Wrap Equipment?
The standard life expectancy of a stretch cover device is typically 5 to 10 years, depending on usage and maintenance. Regular care can expand its life, so maintain an eye on efficiency and address concerns without delay.
Exist Certain Brands Understood for Better Reliability?
Yes, some brand names are understood for their dependability. You'll find that firms like Signode and Lantech often get positive testimonials - stretch wrap machine repair. Investigating individual comments can aid you select a reputable stretch wrap device for your demands
What Are the Signs of Poor Operator Training?
If you notice constant errors, inconsistent covering, or security incidents, those are indicators of poor driver training. Lack of recognizing about maker features or failure to adhere to methods can substantially affect effectiveness and safety and security.
Just How Can I Locate a Professional Service Technician for Repair Works?
To discover a qualified technician for repair services, request for suggestions from industry peers, check online reviews, and verify certifications. You may likewise take into consideration getting in touch with local devices distributors who often have actually relied on service technicians accessible.
Final thought
To sum up, dealing with stretch wrap device repair challenges calls for a positive approach. Do not neglect the importance of solid communication between groups and continual examination of device result.